The Process of Rotomolding: A Guide for Beginners
The Process of Rotomolding: A Guide for Beginners
Blog Article
Rotational molding, or Rotomolding, has turned into a preferred manufacturing approach for producing durable and top quality plastic parts. Their unique method, which involves heating and rotating materials in a very shape, assures consistently spread strength and uniformity in the last product. That blog explores the amazing great things about Rotational Molding and why it's obtained prominence as a strategy for producing tough and long-lasting plastic components.
Superior Energy with Uniform Wall Depth
Among the essential benefits of rotomolding is based on its ability to create components with standard wall thickness. Unlike other production techniques that could keep irregular or thin parts prone to weakness, rotomolding assures consistency atlanta divorce attorneys layer. By equally heat and spinning the shape, the molten resin passes smoothly, making smooth and sturdy plastic pieces that may endure large loads and fight impact.
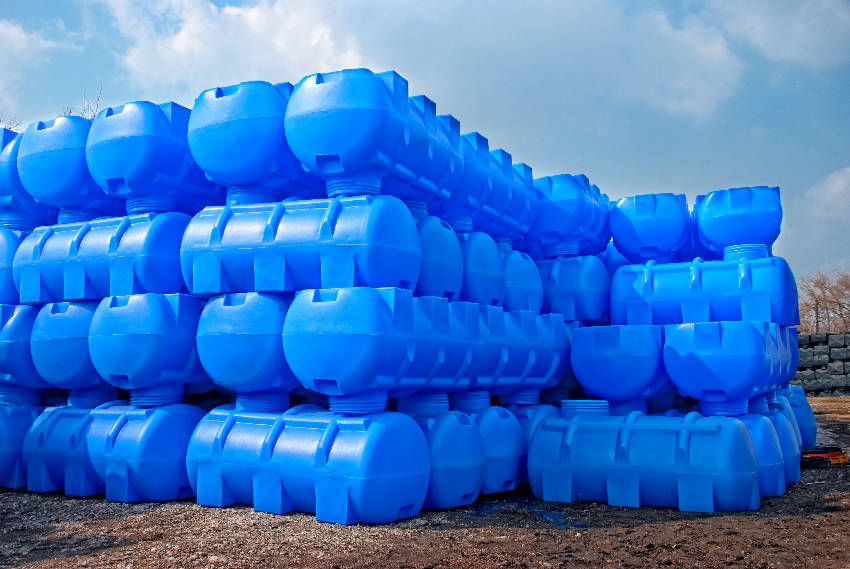
That feature makes rotomolded areas well suited for purposes requesting architectural strength, such as big tanks, playground gear, and industrial containers.
Increased Longevity with Stress-Free Molding
Pressure can destroy plastic areas, impacting their life and performance. Fortunately, the rotomolding process eliminates internal challenges frequently present in other molding techniques. Since number high-pressure forces are utilized throughout generation, the plastic-type activities minimal pressure, resulting in a stronger product that performs easily over time.
Moreover, the absence of stitches or weld lines enhances the general durability of rotomolded parts, making them tolerant to cracking, dividing, and environmental wear and tear.
Outstanding Freedom and Customization
Rotomolding offers unmatched style flexibility, allowing producers to generate complex designs and structures with precision. The capacity to incorporate added features like ribs, positions, or structure assures that the ultimate solution meets certain useful or cosmetic requirements.
This process also supports the use of a wide selection of components and additives, such as for instance UV stabilizers and colorants, further enhancing longevity by making areas resistant to facets like sunlight publicity, diminishing, and compound damage.
Resilience in Serious Problems
Rotomolded components are developed to last, even when subjected to severe environments. They maintain their strength in tough conditions, avoid rust from substances, and experience prolonged outdoor use. That makes them especially useful in industries like agriculture, structure, and underwater programs, wherever components experience demanding problems daily.
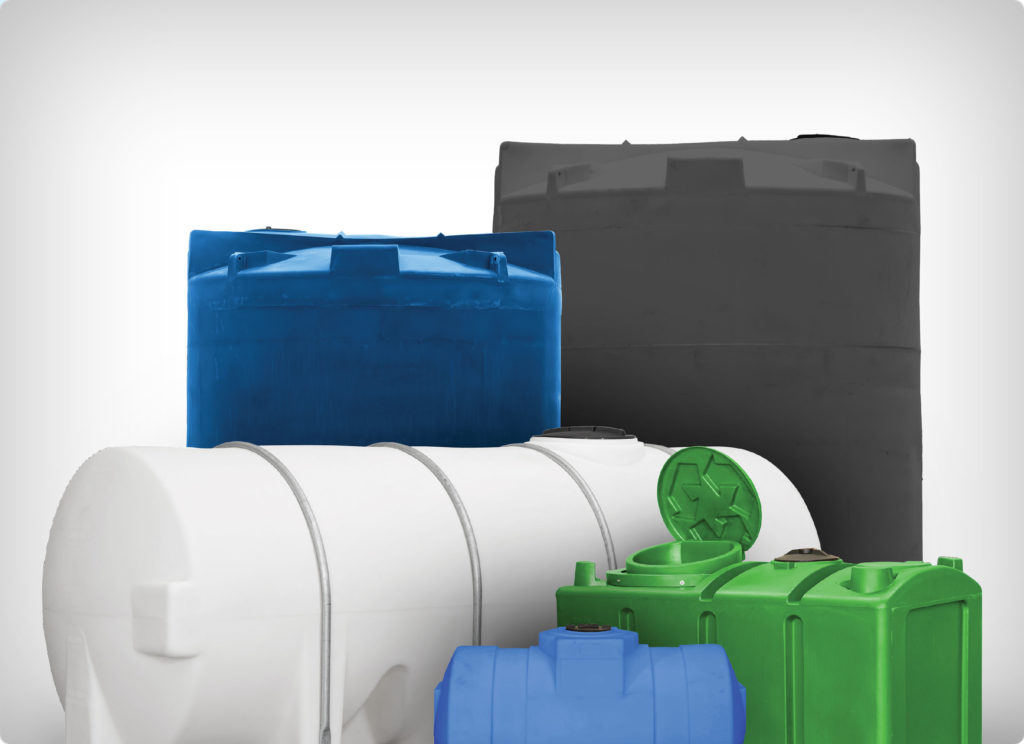
Their power to do dependably in such settings decreases the requirement for frequent substitutes, making rotomolded parts both cost-effective and sustainable.
Driving the Future of Sturdy Materials
The increasing need for reliable and sturdy plastic components continues to put rotomolding at the front of manufacturing innovation. With its precision, stress-reducing benefits, and capability to resist varied conditions, rotomolding is shaping the way in which industries prioritize power and endurance within their products. By purchasing this advanced method, producers may produce plastic components that stay the test of time.
Report this page