How to Choose the Right Materials for Plastics Rotomolding
How to Choose the Right Materials for Plastics Rotomolding
Blog Article
Rotational molding, or rotomolding, has become an essential manufacturing process in today's industry, specially as it pertains to plastics. That adaptable process has permitted businesses across different industries to innovate and generate sturdy, cost-effective, and tailor-made products. But where, exactly, is this method being employed the absolute most? Here's a closer look at the leading purposes of Parts Plastics Rotomolding and the benefits it brings.
What Makes Rotomolding Common for Plastic Services and products?
Before we break up its varied purposes, it's value remembering why is rotomolding stand out. Unlike other production practices, the process consistently directs pockets over the mold for regular wall thickness and superior durability. Its freedom indicates it provides unique types and different industries with ease — the versatility is unmatched.
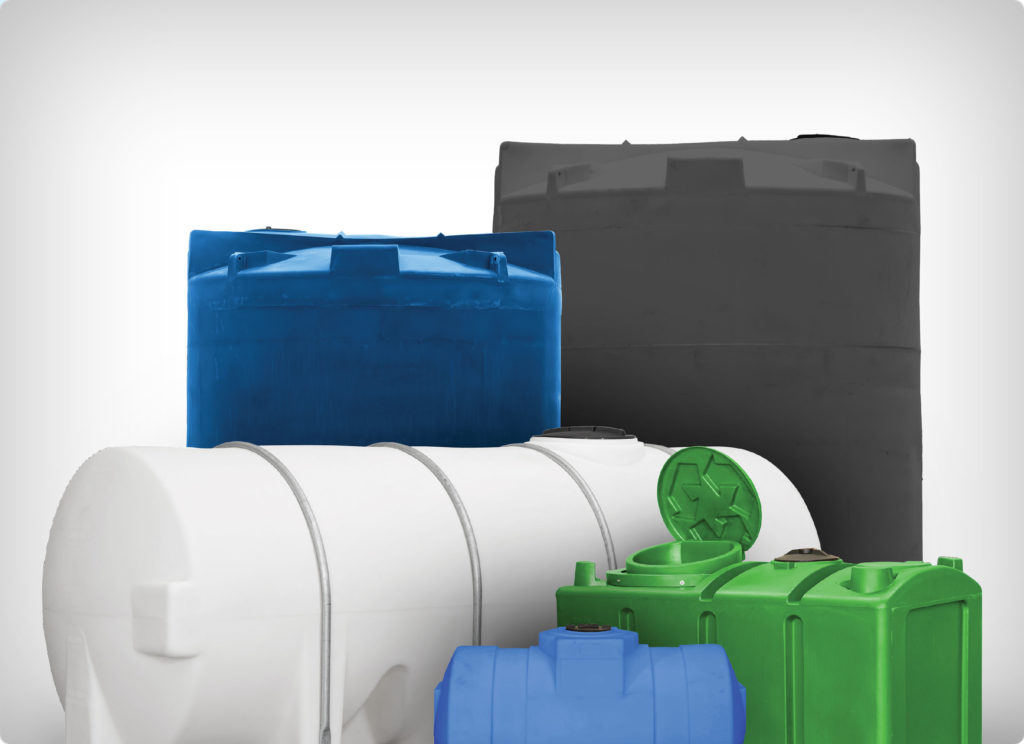
Important Applications of Plastics Rotomolding
1. Storage and Water Tanks
Among the biggest uses of parts rotomolding is in the manufacturing of storage and water tanks. Whether for agricultural, industrial, or residential purposes, rotomolded tanks are prized because of their toughness, resistance to weather conditions, and leak-proof construction. These tanks often feature complex types that benefit from the accuracy of rotational molding.
2. Automotive Parts
From gasoline tanks to air tubes and protective covers, rotomolding represents a significant position in the automotive industry. Automotive components require lightweight, tough, and sturdy resources to enhance car performance, and this manufacturing process provides only that. The capacity to build one-piece, smooth components guarantees long-lasting performance.
3. Outside Furniture and Playground Gear
Creating outdoor furniture and playground components is still another important application. Rotomolding guarantees the products are UV-resistant, resilient against the elements, and secure for many users. For instance, vibrant playground patterns and counter seating take advantage of customization possibilities accessible via this process.
4. Professional Gear
Rotomolded materials will also be widely utilized in commercial controls for parts like hoppers, bins, and machine housing. These components need certainly to experience large use, hard situations, and possible wear. The longevity and power to generate robust elements have located rotomolding as an ideal process for such needs.
5. Customer Items
Everything from kayaks and refrigerators to bins and planters stalks from rotomolding. These customer products and services demand a high-quality, cost-efficient manufacturing technique to make sure durability without reducing design. Rotomolding ticks every box.

The Advantages of Rotomolding
The worthiness of materials rotomolding does not stop at its varied applications. Industries carry on to choose this approach because it:
Allows Customization: Develop delicate styles, styles, and textures unparalleled by different production processes.
Enhances Toughness: Provides seamless, crack-resistant services and products ideal for diverse conditions.
Decreases Costs: Low tooling prices ensure it is a favorable selection for both little and big runs.
Supports Sustainability: Rotomolded products are often recyclable, aiming with the rising push toward eco-friendly practices.
Shaping the Future with Materials Rotomolding
From everyday client items to essential professional instruments, plastics rotomolding stands out as a vital production strategy in today's market. Its adaptability, cost-effectiveness, and longevity assure its extended growth being an industry favorite. Report this page